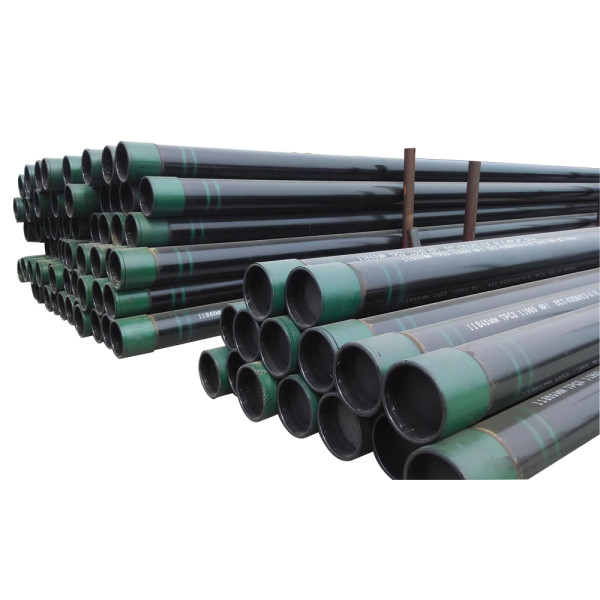
Understanding ERW Pipes
ERW pipes are manufactured using steel coils or strips that are formed into a cylindrical shape and welded longitudinally using electric resistance. In this method, no filler material is used. Instead, the edges of the steel are heated through electrical resistance and pressed together to form a solid bond. The result is a pipe with a visible weld seam, which is often as strong as the rest of the pipe if properly produced.
Understanding Seamless Pipes
Seamless pipes, on the other hand, are made without any welding or joints. These pipes are manufactured through a process called extrusion or rotary piercing, where a solid steel billet is heated and then pierced to create a hollow tube. The tube is then elongated and sized to the desired diameter and wall thickness. Because there is no welded seam, seamless pipes are generally preferred in applications requiring high strength and resistance to pressure or stress.
Differences in Manufacturing Process
The main difference between ERW and seamless pipes lies in their manufacturing. ERW pipes involve a welding process, which makes production faster and more cost-efficient. The welding process is controlled and automated, resulting in high precision and uniformity in dimensions. However, the presence of a weld seam means that additional testing is often required to ensure its integrity.
Seamless pipes undergo a more complex and labor-intensive process. The absence of a weld seam gives them superior strength, especially in handling high pressure and temperature variations. This manufacturing process also allows seamless pipes to be used in critical applications such as nuclear plants, oil drilling rigs, and chemical processing units where the margin for error is minimal.
Strength and Pressure Tolerance
Seamless pipes generally offer higher pressure tolerance compared to ERW pipes. The absence of a seam means there are no weak points, making them ideal for high-pressure applications. In contrast, although modern ERW pipes are strong and reliable, the weld seam can be a potential point of failure if not properly inspected and maintained.
That said, improvements in ERW welding technology have narrowed the performance gap. Today, high-quality ERW pipes can perform comparably to seamless pipes in many standard industrial applications, especially where extremely high pressures are not a concern.
Cost and Production Efficiency
One of the major advantages of ERW pipes is their lower cost. The use of flat steel strips and an automated production process makes them more affordable and quicker to produce in large quantities. This makes ERW pipes a preferred choice for projects where budget and time are key considerations.
Seamless pipes, due to their complex manufacturing and higher material usage, tend to be more expensive. They also take longer to produce, which can affect lead times for large-scale projects. However, their superior strength and durability justify the higher cost in applications where performance and safety are critical.
Dimensional Accuracy and Surface Finish
ERW pipes are known for their consistent wall thickness and smooth surface finish. The automated forming and welding process allows for precise control over dimensions. This makes ERW pipes particularly useful in applications that require tight tolerances and consistent mechanical properties.
Seamless pipes may show slight variations in wall thickness due to the nature of the extrusion or piercing process. Although they offer excellent structural integrity, they may require additional processing to meet precise dimensional specifications, especially in industries such as automotive and aerospace.
Inspection and Quality Control
Quality control is crucial for both ERW and seamless pipes, but the focus differs slightly. ERW pipes require special attention at the weld seam. Non-destructive testing methods such as ultrasonic testing and radiography are often used to verify weld integrity.
Seamless pipes are inspected throughout the length of the pipe, with a focus on material uniformity and internal flaws. Hydrostatic testing, eddy current testing, and visual inspections are part of the standard quality assurance process to ensure these pipes can withstand demanding conditions.
Applications Based on Differences
Due to their lower cost and good performance, ERW pipes are commonly used in water pipelines, fencing, scaffolding, automotive parts, and structural applications. They are also used in low to medium-pressure applications in the oil and gas industry.
Seamless pipes are used where high strength and resistance to pressure are critical. These applications include power plants, petrochemical plants, oil exploration, heavy machinery, and critical structural components. Their ability to handle high stress without failure makes them suitable for challenging environments.
Conclusion
Both erw pipe and seamless pipes play important roles across a wide range of industries. The key difference lies in their manufacturing process, with ERW pipes being welded from steel coils and seamless pipes being formed from solid billets without any welds. This distinction impacts their cost, strength, application, and availability. While seamless pipes offer superior performance in high-pressure environments, ERW pipes provide an economical and efficient solution for general use. By understanding these differences, users can select the right type of pipe to match their technical and budgetary requirements.