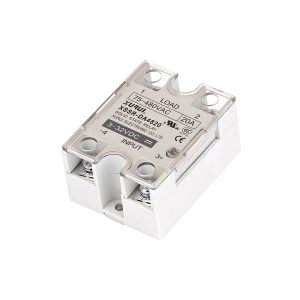
The Role of Limit Switches in Automation
Automation depends on the smooth operation of interconnected systems. Limit switches are electromechanical devices that detect the position or movement of an object. When a moving part comes into contact with the actuator of a limit switch, it triggers an internal change in the electrical contacts. This change can start, stop, or modify the behavior of a machine or system.
Limit switches are used in a wide range of automated processes, from conveyor belts to robotic arms. They send real-time feedback to control systems, such as PLCs or microcontrollers, which then execute the next programmed action. Without limit switches, automation systems would have no reliable way to detect whether components have reached the desired position or completed their assigned motion.
Enhancing Machine Safety with Limit Switches
Safety is one of the most important reasons for using limit switches in industrial and commercial environments. Machines that operate at high speeds or with large forces can pose serious risks if not properly controlled. Limit switches act as safety barriers by detecting the limits of motion and preventing over-travel, which can lead to mechanical damage or worker injury.
For example, in a hydraulic press, limit switches can stop the downward movement of the ram before it hits the bottom or any unintended object. Similarly, in elevators, limit switches ensure the cabin stops at the right floor and prevent it from moving beyond its safe travel range. These actions prevent accidents and contribute to safe machine operation.
In emergency situations, limit switches can serve as triggers for shutdown mechanisms. If a gate or safety door is opened during machine operation, a limit switch can immediately stop the system to prevent harm to the operator. This is why they are often integrated into safety interlock systems, where the machine cannot function unless all conditions are met.
Maintaining Accuracy and Reliability
In automated systems, consistency and precision are crucial. Machines that rely on accurate motion sequences cannot perform properly if their components move too far or not far enough. Limit switches provide this accuracy by offering a definite point of contact that signals when an object or part has reached a specific position.
The repeatability of limit switches makes them reliable over thousands or even millions of cycles. They help maintain process quality by ensuring that each operation, whether cutting, pressing, or aligning, occurs exactly where it should. This is especially important in high-speed production lines where even a small deviation can lead to defective products or production delays.
Adaptability in Different Industrial Environments
Limit switches are designed to work in a wide range of environments. They can function in extreme temperatures, resist exposure to dust, moisture, oil, and chemicals, and withstand mechanical vibration and impact. This makes them suitable for many industries including automotive, manufacturing, food processing, mining, packaging, and material handling.
Because of their durability, they continue to operate reliably in harsh settings where more sensitive sensors might fail. This robust performance ensures that automation systems remain efficient and safe even under challenging conditions.
Simplifying Control System Design
Limit switches simplify the design and operation of control systems. Their straightforward functionality allows them to be easily integrated into new or existing machinery. They can directly control relays, contactors, or logic inputs without the need for complex signal conditioning.
This simplicity also reduces the chances of software errors or system failures. Since limit switches provide clear on/off signals, the control system receives unambiguous instructions about what action to take next. This leads to a more dependable and responsive automation process.
Cost-Effective Safety and Control Solution
Compared to other types of position sensors, limit switches are often more cost-effective. Despite their affordability, they provide a high level of performance and safety. Their mechanical nature means they require little maintenance and have a long service life.
For businesses, this translates to lower total cost of ownership. The initial investment in limit switches pays off through fewer breakdowns, reduced downtime, and improved machine protection. Their reliability also minimizes the need for frequent replacement or recalibration, helping maintain uninterrupted production.
Support for Regulatory Compliance
Many industries are subject to strict safety regulations and quality standards. Using limit switches in critical control and safety functions helps facilities meet these requirements. They can be used to demonstrate compliance with standards such as ISO 13849, IEC 60204, and OSHA guidelines for machine safety.
By incorporating limit switches into your safety system, you show a commitment to protecting workers, preventing accidents, and following industry best practices. This not only protects people and equipment but also helps avoid fines, legal issues, or production shutdowns due to non-compliance.
Limit Switches in Emerging Technologies
As automation continues to evolve, limit switches remain relevant even in advanced systems. While sensors using infrared, ultrasonic, or laser technologies are gaining popularity, limit switches still offer unmatched mechanical reliability. In many cases, they are used alongside modern sensors to provide redundant safety or backup detection.
In smart manufacturing systems, limit switches can be integrated with digital networks to support Industry 4.0 initiatives. Advanced versions with communication capabilities can transmit operational data, such as the number of activations or time in use, to centralized monitoring systems for predictive maintenance.
Conclusion
Limit switches are essential components in modern automation and safety systems. They offer a reliable, precise, and cost-effective way to control machinery, monitor position, and prevent dangerous situations. Whether used for safety interlocks, motion control, or position feedback, these devices contribute to smooth and secure industrial operations.