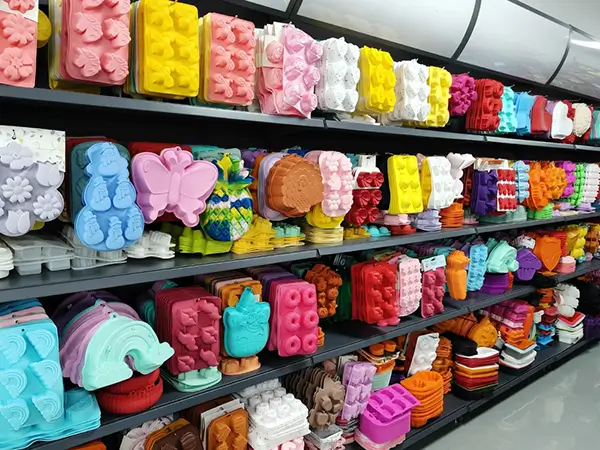
Choosing the right custom silicone mold manufacturer is a critical decision that directly influences the quality, durability, and functionality of the final product. A skilled manufacturer ensures that the molding process is accurate, consistent, and compliant with industry standards. On the other hand, a poor choice can lead to defects, delays, and unnecessary costs.
Understanding the Role of a Silicone Mold Manufacturer
A custom silicone mold manufacturer is responsible for turning a product concept or design into a physical, usable silicone item. This involves various stages such as mold design, prototype development, material selection, and production. The mold itself must be precisely crafted to match the product’s dimensions and tolerances, as any flaws in the mold will be reflected in every product made from it.
Beyond technical ability, a manufacturer’s experience, equipment quality, and attention to detail all contribute to how well the final product performs. In applications where safety, hygiene, or mechanical performance is essential—such as medical devices, automotive seals, or kitchenware—the smallest imperfections can lead to major problems. That’s why selecting the right manufacturer isn’t just a business decision; it’s a quality assurance step.
Impact on Product Accuracy and Tolerances
One of the most important factors in custom molding is how closely the finished product matches the original design. A professional silicone mold manufacturer uses advanced technologies such as CNC machining, 3D CAD software, and precision testing tools to ensure the highest accuracy. They also understand the shrinkage behavior and flow characteristics of silicone during curing.
In contrast, manufacturers lacking these capabilities may deliver products that do not meet the necessary tolerances. Even a small dimensional error can make a seal leak, a medical part unfit, or an electronic cover unusable. This level of precision is especially important for industries where components need to fit or function perfectly with other parts.
Consistency and Repeatability in Production
Another essential reason to work with a reliable silicone mold manufacturer is the ability to produce consistent results in high-volume runs. A well-made mold, paired with a precise manufacturing process, can produce thousands of identical units without defects. This consistency ensures brand reputation, customer satisfaction, and fewer returns or replacements.
Unreliable manufacturers may cut corners on material quality, mold maintenance, or production controls. This often leads to inconsistencies from one batch to another. With consistent production, customers receive exactly what they expect every time—something especially critical when products are sold commercially or used in regulated industries.
Material Quality and Certification Standards
Not all silicone is the same. High-quality silicone can withstand temperature extremes, UV exposure, moisture, and chemicals. Reputable manufacturers work only with certified, medical-grade, food-grade, or industrial-grade silicone, depending on the application. They also provide documentation and testing reports to confirm compliance with international standards such as FDA, RoHS, or ISO.
An experienced custom silicone mold manufacturer will guide clients in selecting the appropriate material based on the intended use of the product. They ensure that the silicone is safe, durable, and suitable for long-term performance. In comparison, manufacturers without quality control may use substandard silicone, resulting in products that degrade, discolor, or fail during use.
Design and Prototyping Support
Choosing a professional manufacturer also means gaining access to their design and engineering support. From prototyping to mold creation, their team can help optimize a product for manufacturing, reducing issues later in production. They can make design suggestions that enhance durability, ease of production, or cost-effectiveness without compromising quality.
This level of support is valuable for startups, small businesses, and companies entering new markets. Without proper guidance, poorly designed molds can result in increased lead times, material waste, or even complete failure of the product. Manufacturers who work collaboratively and communicate effectively add immense value throughout the development cycle.
Long-Term Cost Efficiency
While a reputable silicone mold manufacturer may charge more initially, the long-term benefits outweigh the upfront cost. Better quality molds last longer, require fewer repairs, and produce fewer defective units. This leads to reduced waste, lower replacement rates, and fewer customer complaints.
On the other hand, going with a cheaper but less experienced manufacturer may save money in the beginning but cost more due to rework, shipping delays, and low product reliability. Investing in quality at the manufacturing stage helps companies protect their brand reputation and customer trust over time.
Customization and Scalability Options
Every business has different needs—some may require low-volume production for testing and trials, while others need high-volume manufacturing. The right manufacturer offers scalability and flexibility to grow with your product. They provide customization options such as branding, color matching, and special finishes, helping the product stand out in a competitive market.
A well-established silicone mold manufacturer has the capacity and resources to meet changing demands without compromising on quality. They also adapt to updated regulations, new design challenges, or expanded product lines, ensuring long-term collaboration and growth.
Conclusion
Choosing the right custom silicone mold manufacturer is not just about placing an order—it’s about partnering with a team that ensures your product reaches the highest standard of quality. From design and material selection to production and delivery, every step in the process plays a vital role in how the final product looks and performs.